What’s up guys! There’s been a lot of exciting updates on our test stand, and I’ll let you in on some of the things going on with the structure’s subsystem. Let’s start from the bottom up and talk about how we plan on attaching everything to the ground.
Initially, our plan was to pour out a concrete base on a fixed spot where we would have to go to test every time. It would have metal rods coming from it, which would allow our stand to be bolted down and secured to the concrete base. This also worked well since we wanted a design that would allow us to keep our stand safe and dry after testing, and would only require a forklift to put it in place and take it away after a day’s work. However, we had a better idea: a trailer. The trailer would allow us to be even more mobile, without requiring a fixed base to return to every time. We’re free! It also doesn’t require a forklift to move our stand around which is a big plus, only a car that we can attach the engine to.
Now onto the engine mount. We initially had the engine attached to the blast shield, sending the load through a box steel beam welded all the way to the back of the stand, where the force would be dissipated in the ground. A simpler way of achieving the same outcome is with an I-beam which will be attached to the frame of the trailer. The I-beam has many advantages, the 2 biggest ones being that it will absolutely not bend, at least not with the 1100 lbf we plan on applying to it, and it allows us to ditch the box steel beam that we had before, thus isolating the engine mount from the rest of the system, decreasing complexity, and making us much safer as well :).
Finally, let’s talk about the actual structure. Remember when I mentioned a welded box steel beam when talking about the engine mount? Yea, not anymore. With the engine now being entirely separate from the rest of the stand, structural integrity becomes much less of a concern, so we started exploring options. 80/20 was the perfect candidate, being much cheaper, lighter, and easier to assemble than the previous box steel structure. The 80/20 beams will not only save us a lot of money with the material itself but with getting professional welding or training to do it ourselves. We can now build the majority of the structure by hand, in-house, with no welding required, as we now only need to bolt the entire structure together. Without needing to drill any holes, the 80/20 also gives us a lot of leeways when it comes to making mistakes, as anything that may be put together by mistake can just as easily be loosened and fixed. Awesome!
We have started ordering materials, and we actually have the rectangle where the engine mount will sit, so it seems like we’re on track to finish this ahead of schedule.
That’s all I had to say, don’t forget to follow us on Instagram to keep in the loop about what goes on in our team.
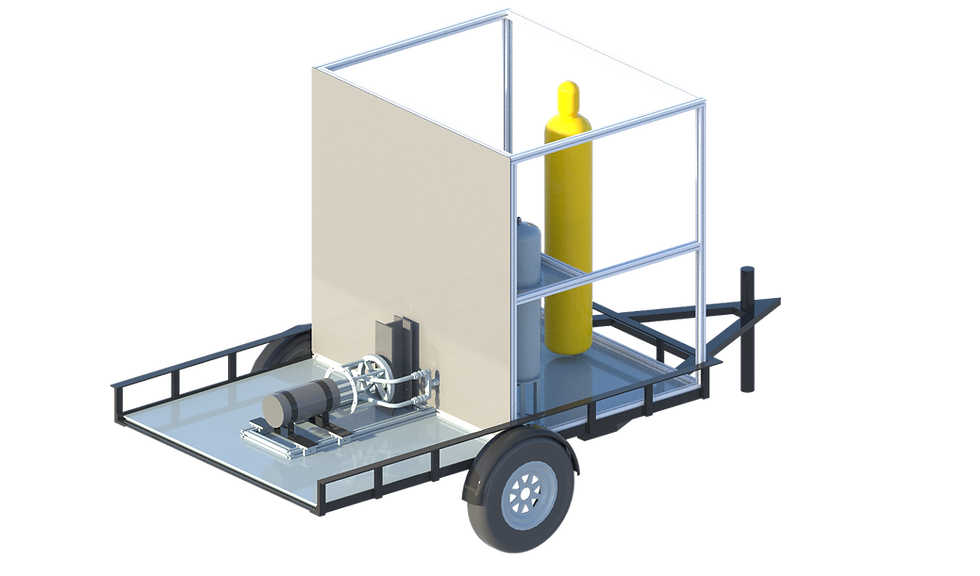
Comments